Quality Circles: The U.S. False Start to Lean
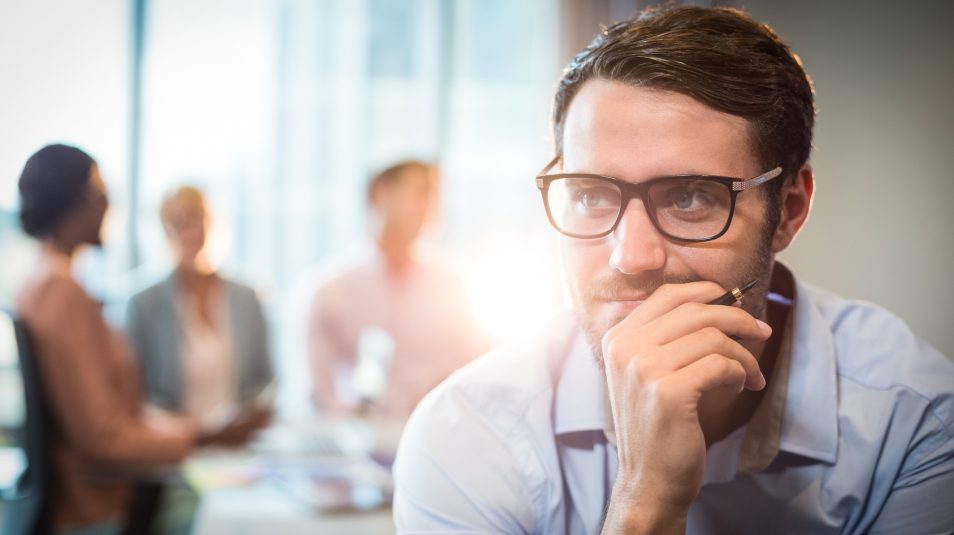
(This is the fifth in a 12-part series on the origins of Lean in the U.S. and my role as one of its pioneers.)
It was clear that employees in Japan were engaged. Toyota was famous for andon, a manufacturing term used to describe a system whereby employees could “pull the cord” and alert management and engineering that there was a quality problem. Pulling the cord resulted in the production line coming to a stop and causing all resources to be focused on resolving the problem all the way back to its root cause.
YouTube: Why Buy a Toyota – Andon Cord
In the U.S. we used inventory to hide these kinds of problems. If there was a problem with a part we had an extra batch of parts around and would set the bad one aside for the quality department to analyze. But in Japan a quality problem caused immediate focus on problem solving and a drive to eliminate all quality problems at their source. It was a philosophy of “build quality in” versus an “inspect bad quality out” approach.
Read More....