Five Reasons Job Seekers Should Study Lean Management
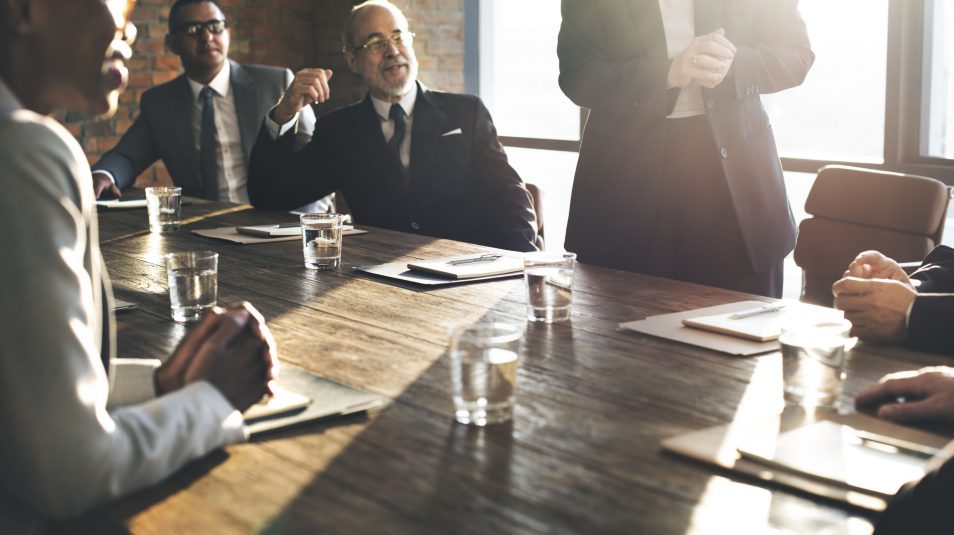
Even seasoned senior managers look to continually enhance their skill sets to differentiate themselves from other job seekers.
Management job seekers with lean management experience can separate themselves from the competition.
Those who study lean management demonstrate to employers an understanding of the forces of the global economy, as well as the requisite lifelong learning for business success. Here are five reasons:
Companies Invest in Lean Management, Creating Lean-Related Jobs
GE initially invested $432 million in the United States to develop “centers of excellence” that practice lean manufacturing. This was just the start. With digitization, information speeds up processes, enhancing the ability for rapid decision-making.
GE responded to the need for speed by implementing what is termed “FastWorks,” a framework which takes lean to the next level. And numerous companies followed this lead.
Job seekers who independently seek lean management training will stand out not only for their skills, but for their ability to anticipate a future employer’s needs.
Lean Allows Managers to Consider Accepting a Position with a Failing Company
In general, job seekers attempt to avoid struggling companies. Lean managers, on the other hand, have the flexibility to look for employment with companies that experience significant business challenges.
Applicants with a deep understanding of lean may identify companies where an overhaul of manufacturing can reverse a failing company. Lean management simply expands the opportunities for job seekers qualified for senior executive positions.
Continuing Education Fills Gaps in a Resume
Employers have always been reluctant to hire an individual who has been unemployed for an extended period. Most hiring managers will not exclude unemployed applicants, but a period of idleness never reflects well on a candidate.
Lean management training allows job seekers to avoid resume gaps at a fairly minimal expense, without the need to seek a degree. Junior and mid-level managers may even consider interning with a lean shop.
Where High Turnover Exists Process-Oriented Managers Are in Demand
For a people-oriented manager, the loss of experienced employees may prove insurmountable. Lean managers tend to be process-oriented: They focus on developing processes which can create success, even with decreased staffing.
Lean managers are not necessarily callous, or uninterested in the employee success. On the contrary, lean often helps companies avoid layoffs that could have otherwise have been necessary. A process-oriented manager can enter a struggling department and use lean principles to develop processes that make each person’s job easier and more clearly defined, while preparing the department to weather future turmoil.
A Lean Manager Emphasizes Value
A job-seeker fluent in lean would present quite an argument for hire if they can effectively communicate why they studied lean: To learn how best to maximize customer value and minimize waste. Because in the global marketplace, others are aggressively looking at your market share and working out how to take it.
Peter Anthony is President & Chief Executive Officer of UGN, which he joined in 1992 as sales and marketing manager. Upon taking the helm of chief executive in 2002, Anthony ultimately reinvented UGN—expanding it from a niche supplier to a broad-based corporation with a diversified product line. His drive to embrace the Toyota Production System as the foundation of the UGN business model resulted in maximum productivity and efficiency throughout his manufacturing and business management structure. Today, Anthony spearheads the company’s more than $400 million in revenue across six manufacturing facilities in the United States.