It Really Isn't a Tradeoff
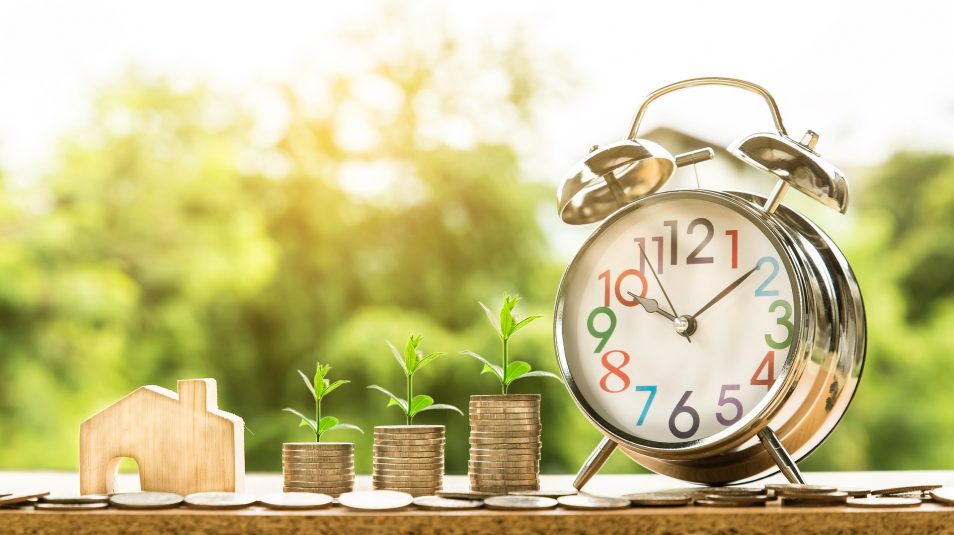
For a long time it was a commonly accepted belief that cost, quality and time were opposing choices. The belief was that they traded off against each other because good quality took lots of time, speed increased cost, and costs had to be higher if you wanted the quality right.
Strangely enough these beliefs were surviving folklore from the craftsman era. For example, back then the belief was that creating a handmade leather saddle took extra time and cost extra money in order to possess the high quality expected of a custom saddle. In that world this is still true.
Most of us don’t live in the one-off world anymore. Most products we buy and services we use are provided en masse. Even if they are customized to our needs, as a Starbucks cup of coffee is, most products and services are still mass produced.
Read More....
[…] Posted in Change ManagementLeadership Developmenthttp://www.massingenuity.com/2012/10/08/it-really-isnt-a-tradeoff/For a long time it was a commonly accepted belief that cost, quality and time were opposing choices. […]
Hi John,
You put forward a strong argument for those of us managing teams involved in routine operations (characterized by high-volume repetitive work), but what about the complex and innovation operations that also exist within most large organizations and in which many of us find ourselves involved in and managing?
For example, seeking greater efficiency through continuously improving already well-established processes translates easily from a manufacturing context to an accounting department, but improving efficiency alone does not lead to better outcomes in situations that require effective communication and problem solving across multi-disciplinary teams. Such situations do not involve repetitive operations, particularly in situations where team goals evolve over time and team membership is constantly changing. In these situations, quality and efficiency are not the most important factors for determining effectiveness (consider, for example, operations at NASA and the two arguably preventable shuttle disasters).
Amy Edmondson put forward a very useful model which describes work in terms of the “Process Knowledge Spectrum” – I wonder if reference to Amy’s work could be employed to expand your argument beyond the metaphor of mass production?
At one end of Amy’s model, we have the “Routine Operations” of mass production, as well as any work that is predictable, well-defined and repetitive (such as the work of an accounting department) and in which failures are caused primarily by deviation, inattention, or process inadequacy. Such routine operations can be effectively managed through appropriate training and monitoring quality.
In the middle of the “Process Knowledge Spectrum,” we have “Complex Operations” characterized by teaming across distance, cultural, and status boundaries, and across disciplines – consider all the junior and senior people across multiple disciplines that come together from different organizations to design a building, run a humanitarian relief effort, or deliver health services in a hospital system. Even in large multi-national manufacturing firms, complex operations exist whenever a cross-operational task-force is formed to address a specific strategic challenge.
At the far end of Amy’s model, lie “Innovation Operations,” the bleeding-edge R&D departments, where “failure” has a very different meaning from failure in routine operations – in fact, there are typically very many failures before a viable product emerges. Sometimes, failures in innovation operations are even re-tasked as new unexpected offerings: Amy reports that “…Pfizer’s lucrative Viagra was originally designed to be a treatment for angina…”, for example.
Admittedly, it’s no surprise that a one-size-fits-all approach to quality and efficiency falls apart when we consider contexts beyond the subject of your post (efficiency in mass production and routine work processes). But I’d be interested to read your thoughts on these other contexts.
For more on Amy’s excellent work on improving the effectiveness of teams across contexts from mass production, to multi-discipline collaboration, to cutting edge research and innovation, refer to: “The Competitive Imperative of Learning,” HBR, July 2008 http://hbr.org/2008/07/the-competitive-imperative-of-learning/ar/1 , “Strategies for Learning from Failure,” HBR April 2011 http://hbr.org/2011/04/strategies-for-learning-from-failure/ar/1 , and “Teaming: How Organizations Learn, Innovate, and Compete in the Knowledge Economy,” Jossey-Bass, 2012 http://amzn.com/078797093X .